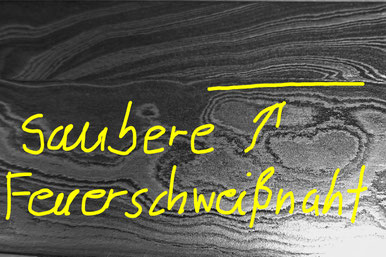
Tja, so sollte ein Damast aussehen. Geht man hier mit der Lupe oder dem Mikroskop ran, dann findet man keinen Schweißfehler. Alle Schichten sind feuerverschweißt. Trotz der verwendeten hochlegierten Stähle sind auch beim Torsionsstrang keine Risse oder offenen Lagen zu erkennen.
Jetzt kennt jeder Damastschmied den Augenblick in dem er feststellt, "hier läuft was gehörig schief!"
Normalerweise bekommt man auf Webseiten über Schmiede schöne Fotos von den Glanzstücken der Produktion zu sehen. Darf aber jeden angehenden Schmied beruhigen, es klappt nicht immer so wie man sich das wünscht. Besonders beim Damast schmieden werden auch erfahrene Schmiede ab und zu aus dem "Olymp" stürzen.
Möchte hier ein treffendes Zitat von Maik Salzmann anbringen:
"Beim Damast schmieden lernt man immer wieder Demut gegenüber dem Material!"
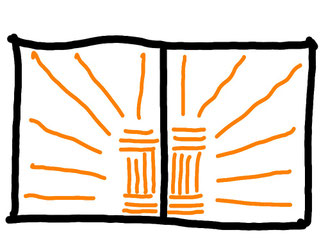
Das mit dem Olymp ist so eine Sache. Zeus würde auch nicht auf einen Maik hören, wenn der ihm was von Demut predigt, oder?
Richtig! Wir auch nicht! Will mal das Ergebnis vorweg nehmen:
"Merke dir den Satz vom Maik!!!!!!!!!!!"
So, im Bild siehst du die Grundidee eines Mosaik-Damastes, welcher dann gehörig in die Hose ging.
Die orangen Strahlen sollten eine stilisierte aufgehende Sonne darstellen. Diese "Damast - Sonne" wäre dann in einem großen Küchenmesser schön eingearbeitet worden.
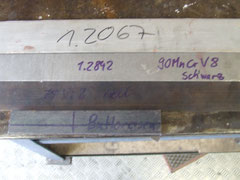
Als Material haben wir zu den auf dem Bild gezeigten Sorten noch eine alte Feile hinzu genommen.
Die orangen Linien in der Skizze entsprechen dem Nickelstahl.
Zuerst wird der rechteckige Mittelbereich als Schichtdamast hergestellt, danach der Feilenstahl (schwarze Färbung) auf den Kernbereich aufgeschweißt und dann die Nickelstahlstrahlen eingearbeitet.
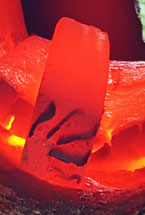
Sieht eigentlich nicht schlecht aus, was da so im Ofen liegt. Bis zu diesem Zeitpunkt war eigentlich auch noch alles im grünen Bereich.
Die Schichten haben sich sauber Feuerverschweißt und die Form entspricht der Skizze.
Dann kam der Übermut!
Ist ja schön wenn sich das glühende Eisen so mir nichts, dir nichts in die gewünschte Form klopfen lässt, aber.......
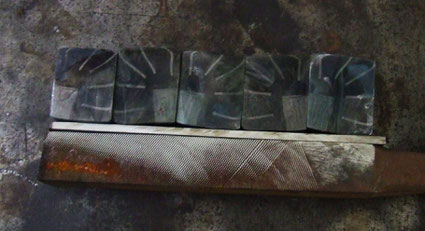
Fehler 1:
Wenn man sich schon die Mühe macht einen Damast zu schmieden, dann nimm dir Zeit!
Hab ich nicht gemacht. Hätte ich mir Zeit genommen und sorgfältig gearbeitet, dann hätte ich die Vierkant-Damast-Klötze sauber winkelig geschliffen, damit keine Spalten sichtbar sind. Die Lücken zwischen den Klötzen laden förmlich Schweißfehler durch Oxidschichten und Verunreinigungen ein.
PS: Falls du dich jetzt frägst, wie haben die Chaoten die Feuerverschweißung trotz der Spalten hinbekommen, dann liegt das an der Lehm- und Stroh-Mischung :-)
An dieser Mischung haben wir fast ein halbes Jahr rumgefeilt. Damit lassen sich aber manchmal Dinge machen, die mit Borax oder Sand weit außerhalb des Möglichen sind. (siehe auch den Punkt Erde)
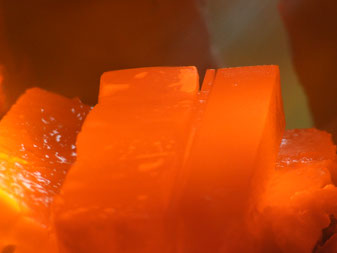
Fehler 2:
Überschätze dich nicht, gehe Schritt für Schritt vor!
Zuerst hätten die Klötze feuerverschweißt gehört, bevor sie dann auf die Feile mit der Nickelstahlschicht aufgeschweißt werden können.
Aber "Nein", man meint ja ,man kann das gleich in einem Aufwasch machen. GEHT NICHT!
Da wir komplett mit Hand schmieden, also keinen Maschinenhammer haben, durchdringen wir mit unserer Schlagenergie den Damast nur bis zu einer bestimmten Materialdicke. Ist das Ausgangsmaterial zu dick wird nur ein Teil des Damastpaketes verformt, der Rest bleibt fast in seiner ursprünglicher Form. Es entstehen "Spannungen und Verzerrungen im Gefüge des Stahls"!
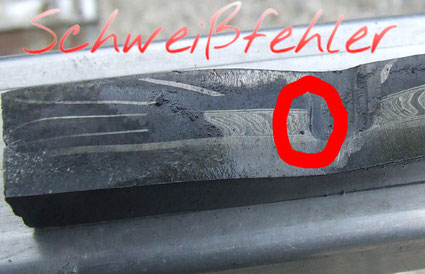
Fehler 3:
Bei solch einem Mosaikdamast solltest du nur Material nehmen, welches du schon oft geschmiedet hast und du dir schon im Vorfeld ein Bild machen kannst wie es sich verhält.
Nicht gemacht!
Hab einen Feilenstahl verwendet, der sich wesentlich stärker verformt hat als erwartet. Dadurch wurde die Feuerverschweißung der Klötze auf der Oberseite extrem erschwert. Auf der einen Seite mussten wir mit extrem harten Schlägen die Klötze verschweißen, auf der anderen Seite führten eben diese Schläge dazu, dass das Feilenmaterial sich zu schnell "streckte". Natürlich sind die harten Schläge nicht für das Muster förderlich. Kurz gesagt, oben sollte es zusammenbleiben, aber unten ist es zu schnell auseinander gegangen. Folge: Mussten einen Keil in den Damast einarbeiten um die Lücke zu schließen. Damit Schweißfehler eingehandelt und das Muster der stilisierten Sonne zerstört.
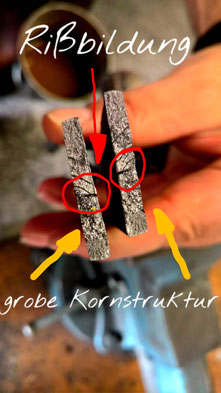
Jetzt war das "Kind" eh schon in den Brunnen gefallen und die Lust am "Blödsinn machen" geweckt.
Fehler 4:
Jetzt haben wir ja verschiedene Stähle im Damastpaket eingearbeitet, einige davon hochlegierte Stähle. Das Problem an diesen Stählen ist ihr relativ schmaler Temperaturbereich in denen man sie schmieden kann. Ist man zu schnell mit dem Erhitzen riskiert man Risse. Das gleiche geschieht, wenn bei einer zu kalten Temperatur geschmiedet wird. Die verschiedenen Stähle verformen sich dann bei jedem Schlag mit dem Hammer so unterschiedlich, dass es zu immensen Spannungen kommt. Die Folge ist dann z.B. Rißbildung an den Korngrenzen oder an den Schweißnahtstellen der unterschiedlichen Stähle.
Hört man dagegen bei einer zu hohen Temperatur mit dem Schmieden auf, so führt dies zu einer Grobkornbildung. Der Stahl verliert dadurch seine guten Eigenschaften (Festigkeit, Elastizität, Härte, Schnitthaltigkeit...), er wird spröde.
Hier sieht man auch ganz gut das Dilemma beim Damastschmieden. Es wird immer ein Kompromiss in der Temperaturführung des Damastpaketes nötig sein. Einen Idealtemperaturbereich zum Schmieden kann nur für einen Monostahl ermittelt und eingehalten werden.

Fehler 5:
Jetzt haben wir gerade was von hochlegierten Stählen gehört. Diese haben noch eine Problematik, welche oft "übersehen" wird. Diese Stähle leiten Wärme nicht so gut wie Eisen oder niedriglegierte Stähle. Das Damastpaket erscheint außen als heiß genug, aber leider nicht im Innern. Einmal nicht richtig durchgewärmt und schon...?
Richtig! Risse!
Fehler 6:
Risse, Risse, Risse,... Oftmals stellt man das Elend erst beim Härten fest und bekommt dann so eine richtig gute Laune. Eine gute Möglichkeit ist es sich die möglichen Verformungen des Materials immer vor Augen zu halten. Lässt man dieses Wissen gleich in die Grundgestaltung eines Damastes einfließen und sorgt beim Aufbau der Schichten gleich dafür das Spannungen bestmöglich vermieden werden, dann schränkt man die mögliche Rissbildung gewaltig ein. Für unser Vorhaben hat dies zur Auswirkung gehabt, dass durch die Wahl des Sonnenstrahlenmotives eigentlich eine starke Umformung sich verbat.
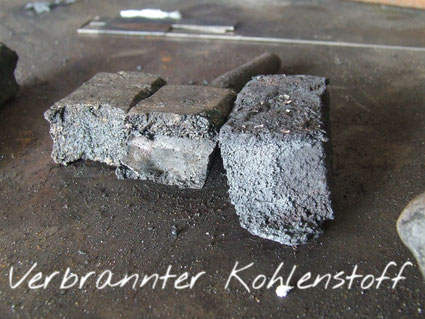
Fehler 7:
Jetzt hat man sich so einen Riss eingefangen und steht nun vor der Esse.
Was machen?
Es bleibt die Möglichkeit der "Überhitzung" beim Feuerverschweißen. Wie es schon der Name sagt, es wird dem Stahl zu heiß, somit werden auch seine Eigenschaften negativ beeinflusst. Der Grat für eine "erfolgreiche" Überhitzung ist extrem schmal. Nur wenige Grad über der kritischen Grenze und der Kohlenstoff verbrennt. Das Ergebnis sieht dann nicht mehr ganz so vielversprechend aus. Da bleibt dann nur noch der Schrott!
Im Bruchtest erkennt man dann grobe Kornstrukturen. Wenn man dann noch mit dem Mikroskop hinschaut, erkennt man an den Korngrenzen den "ausgelösten" Kohlenstoff, welcher an den Stellen mit Sauerstoffkontakt verbrannt ist.
Zum Schluß:
Der beste Rat, den ich dir geben kann ist, NIMM DIR ZEIT!
Arbeite zuerst mit den einzelnen Stahlarten getrennt um ein Gefühl für das Material zu bekommen. Plane die einzelnen Arbeitsschritte genau vor und bleibe bei der Arbeit immer konzentriert!
Trotzdem, Spaß macht es schon, sich auf "unbekanntem Land" zu bewegen und einfach mal auszuprobieren. Wenn mal was schief geht, egal! Denke darüber nach und du hast extrem viel für das nächste Mal dazugelernt!
Interessante passende Literatur:
Für alle die sich ans Damastschmieden ranwagen wollen, hier noch ein Link zum Artikel