
So, hallo!
Das Messer kennst du vielleicht schon. Schleppen wir auch fast auf jede Veranstaltung und Ausstellung mit.
Wenn wir es dann immer mit stolz geschwellter Brust und funkelnden Augen präsentieren, dann kommt unwillkürlich die Frage : "Was ist denn das Besondere an diesem Messer?"
Zuerst aber kurz zum Gedanken, welcher dem Messer zu Grunde liegt. Es sollte ein absolut alltagstaugliches und robustes Messer herauskommen, das auch dem Lageralltag auf einem Pfadfindertreffen gewachsen ist. Gemüse, Zwiebeln, Fleisch und Brot schneiden, wenn es sein muss auch im Blechnapf. Kleinholz zum Anzünden machen, Dosen öffnen, Schnitzen und Nutella auf ´s Brot schmieren. So ein Messer sollte also am Ende rauskommen!
(1. Grund)
Ein profaner Grund warum wir stolz auf dieses Messer sind ist der Umstand, das es das dritte Messer, welches wir bis dahin gefertigt haben, ist. Gleichzeitig auch der dritte DAMAST.
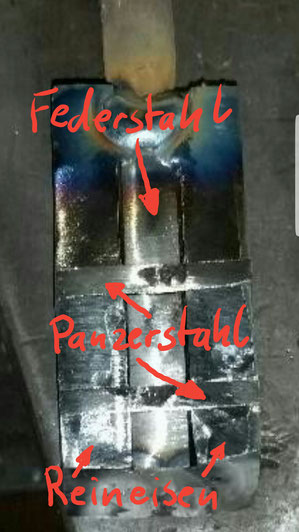
Jetzt sind wir schon mal beim Thema Damast. Bei der Auswahl der Materialien für die Schichtung war die Grundidee für das Messer von Bedeutung. Es mussten Materialien sein, die auch eine Schockbelastung aushalten und trotzdem noch eine relativ gute Schnitthaltigkeit haben.
Kurz im Materiallager rumgestöbert und folgende Wahl war getroffen:
- Federstahl (Härtbar, Schockbelastbar)
- Panzerstahl (extreme Härte und Zähigkeit)
- Reineisen ( wenig korrosiv, weich)
Zur Schichtung:
Eigentlich war nur ein normaler Schichtdamast geplant. Mit dem Panzerstahl hatten wir davor schon einige Erfahrungen gesammelt und uns wirklich den "Hannes" abgeklopft!
Irgendwie war der Schichtdamast "langweilig", deshalb musste was anderes her. Wir haben dann zwei Panzerstahlstreifen lose in Querrichtung in das Damast-Grundpaket geschoben.
Der Gedanke zum Schmiedevorgang:
Uns war bewusst, wenn man beim Feuerverschweißen auf die Längsseite draufklopft, dann drückt es uns die Querschichten aus Panzerstahl aus dem Verbund und es entsteht keine Schweißverbindung. Wir wollten zudem, dass sich der Panzerstahl so um die Längsschichten legt, damit er diese wie eine U-Klammer zusammenhält und "verstärkt".
Beim Schmieden:
Ein erster Probelauf mit einem anderen Material ging grandios daneben. Wie befürchtet wurde die Querschicht aus dem Verbund "gedrückt". Wenn man es richtig sagen will, dann ist die Querschicht quer durch die Werkstatt geschossen! :-)
Wir haben aber einiges dabei gelernt und die komplette "Schlagtechnik und -abfolge" überarbeitet. Auch die Hitzeverteilung in der Kohleesse wurde geändert.
(2. Grund)
Mit neuer und unkonventioneller Schlagtechnik, Feingefühl und präzisen Schläge haben wir das Paket ohne Schweißfehler feuerverschweißt!
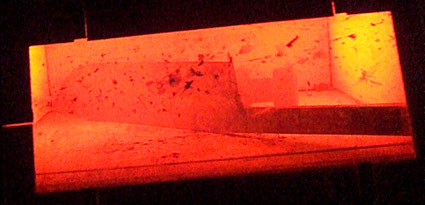
Jetzt ist es ja der normale Weg einen Messerrohling soweit vorzufertigen, dass nach dem Härten nur noch sehr wenig geschliffen werden muss. Oft lässt man auch ein bisschen mehr Material zum Schleifen am Rohling um einen Härteverzug noch ausgleichen zu können.
Insbesondere bei meinem Geschmack für dünne Messer ist ein Verzug leicht möglich.
Hier haben wir den Messerrohling bis auf die Schneide komplett geschliffen und poliert. Um dem Härteverzug zu verhindern ruhte die Hoffnung auf dem "U-Panzerstahlklammern"-Aufbau des Damastpaketes.
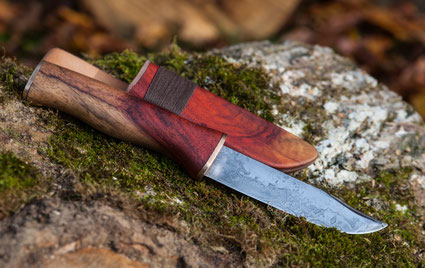
(3. Grund)
Die Klinge hat nach dem Ölhärten keinen Verzug! Das Einzige, was nach dem Härten gemacht wurde, ist die Schneide schleifen und die Oberfläche mit Stahlwolle blank polieren.
Hierdurch konnten wir die Maserung der Damastklinge ohne Ätzen herausarbeiten. Streicht man über die Klingenflanke kann man die "Höhen und Täler" der verschiedenen Stahl- und Eisensorten spüren. Diese Musterung entsteht durch das unterschiedliche Schrumpfverhalten der Sorten beim Härten. Ein unbeabsichtigter Vorteil ist auch noch, dass wir die hauchdünne Oxidschicht an der Oberfläche nicht abschleifen mussten. Diese Schicht macht das Messer sehr korrosionsbeständig!
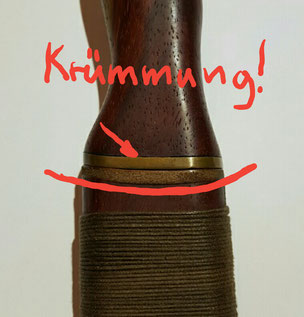
Dem Ein oder Anderen ist der Bereich des Rapierstücks aufgefallen.
(4.Grund)
Sonst wird das Rapierstück gerade und eben gefertigt. Damit geht man den meisten Problemen aus dem Weg, aber irgendwie passt das nicht so richtig zu den Krümmungen des Griffes und der Scheide. Die Anpassung der einzelnen gekrümmten Bauteile erfolgte in "Freihand", sprich ohne Führungen oder sonstige Hilfsmittel!
Auch wurde die Klinge ohne Ricasso (Fehlschärfe / Dies ist der Teil der Klinge, welcher üblicherweise als Rechteck in das Rapierstück mündet.) und Schleifkerbe gearbeitet. Somit musste der Spalt des Rapierstückes der Klingenform angepasst werden. Hier war der sich bis zur Schneidkante verjüngende Bereich sehr schwierig auszuarbeiten um einen unschönen Spalt zu vermeiden.
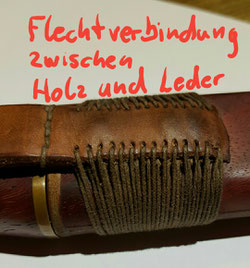
(5.Grund)
Zum Schluss noch die Holzscheide und die Anbindung der ledernen Gürtelschlaufe.
Uns gefällt die Flechtverbindung und die Kombination von Leder mit Holz im Messerscheiden-Aufbau stellt gleichzeitig eine Premiere dar. Das erste Mal haben wir Leder in dieser Art verarbeitet und vernäht.
Du siehst an der Länge des Artikel das uns dieses Messer am Herzen liegt. Übrigens, unser Logo "TS", was du auf unserer Webseite immer siehst stammt vom Griffende dieses Messers.
Das Jagdmesser TS-1 würden wir jetzt wahrscheinlich in einigen Details anders ausarbeiten, aber es zeigt exemplarisch den Grundstil unserer Messer. Es ist also sozusagen der Grundstein unserer Messerfertigung!
Im Gebrauch hat mich dieses Messer noch nie in meinen Erwartungen enttäuscht. Dies ist auch das oberste Ziel der Produkte aus der Telchinen-Schmiede.
An erster Stelle steht der Nutzen und die Gebrauchsfähigkeit!
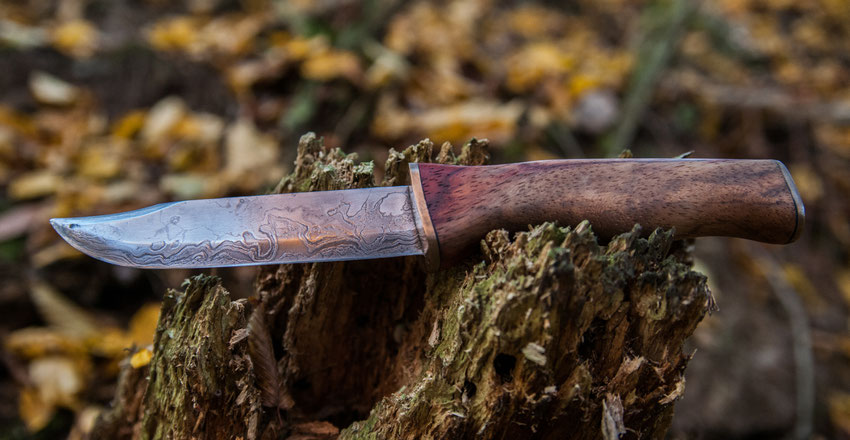
Daten zum Messer
- Damast: 80-Lagen mit Längs- und Querschichtung!
- Gesamtlänge: 275mm
- Klingenlänge: 125mm
- Klingendicke: 2,5mm
- Messergewicht ohne Scheide: 159g
- Gesamtgewicht: 273g
- Handfertigung: 34h
Du findest weitere Informationen zur Herstellung in unserem Artikel Panzermesser.